ドリル穴あけ:歩行現象によるおむすび形状を防げ!丸い穴を開ける方法!
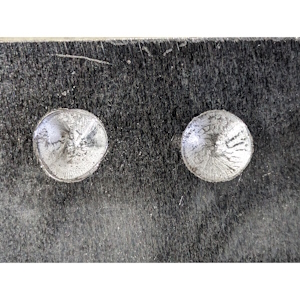
一般用鉄工ドリルで丸い穴を開けるための究極の手引き
おむすび三角形、または五角形になってしまうドリル歩行現象の原因の説明とその対策法を紹介しています。
目次
おむすび穴?
鉄工ドリルで穴を開けているとき、加工の初期段階において、その形状が五角形や、三角形のおむすび・・・おにぎりのようになったことはありませんか?
ほら、こんな風に・・・
五角形型
三角形型
おにぎり・・・
裏切りおにぎりはともかく、ドリルの断面は丸いのに、なぜ三角形や五角形のいびつな穴になってしまうのでしょうか?
これは、ドリルの振動やビビりによって引き起こされる「歩行現象」が原因と考えられます。特に、一般的な2枚刃のツイストドリルでは、歩行現象が発生すると穴が三角形や五角形に歪んでしまうのです。
ドリルの歩行現象については、多くの研究報告が存在しますが、その内容は非常に難解です。そこで今回は、既存の研究に加え、当方の検証結果も踏まえた上で、簡潔なまとめを解説していきます。
<検証準備>
検証用のドリルは、株式会社不二越のナチ(NACHI)のストレートシャンクドリルです。ドリル径は小さすぎず大きすぎない9.5mmにしました。シンニングなしのものです。
<切削条件>
回転数と送り量:745min-1、0.15 mm/rev
被削材:SS400板厚9ミリ
検証1:新品のドリルでの歩行現象
逃げ角は約15°でチゼル角は約130°ぐらいでしょうか。
逃げ角が大きいですね。刃が立ちすぎています。メーカーにもよりますが、新品のドリルにありがちです。
以下のように、逃げ角が大きいとビビリも発生していることが分かります。切り刃が薄くなるので切れるドリルではあるのですが、振動が発生するうえ刃が欠けやすいです。そのままでは使いづらいですね。
検証2:先端角の変化による歩行現象への影響
検証2では、逃げ角とチゼル角は同じで先端角のみ変化させました。左のドリルビットからそれぞれ100°、118°、135°の先端角です。
結果は、どの先端角でも良い形になり、歩行現象は先端角の違いにほとんど影響されないことが分かりました。
先端角100度 | 先端角118度 | 先端角135度 |
![]() |
![]() |
![]() |
※逃げ角は約10°チゼル角は約115°
※正確な研磨を行なう必要があるため、手研ぎではなくドリル研磨機を使用しています。
※検証結果画像は、いずれも穴深さ約4mmまで加工し、穴の口元から穴の底面を覗いたものです。
検証3:チゼル角の変化による歩行現象への影響
検証3では、先端角はいずれも118°で、チゼル角のみを変化させました。左のドリルビットからそれぞれ約100°、約120°、約130°のチゼル角です。
チゼル角110度 | チゼル角120度 | チゼル角130度 |
![]() |
![]() |
![]() |
結果は、差が大きく出て、チゼル角が小さいドリルの方が歩行現象が抑えられていることがわかりました。チゼル角130の穴はおにぎりになっちゃってますね。ただ、チゼル角が変わるとチゼル幅も変わるため、大きいチゼル角の場合はチゼル幅が長くなることに留意する必要があります。
検証4:送り量の変化による歩行現象への影響
送り量は左から「0.05mm/rev」「0.15mm/rev」「0.30mm/rev」です。
以下の画像のように送り量を大きくしていくと真円度が増していることが分かります。
ドリル加工での送りについて
ドリル加工において、「送り」とは機械が工具を移動させる距離を指します。送りの表し方には、以下の2つの表現があります。
1.送り速度(Vf)
単位:mm/min
意味:1分間に工具が進む距離を示します。
例:1分間に工具が進む距離が100mmであれば、送り速度は100mm/minです。
2. 送り量(f)
単位:mm/rev
意味:工具が1回転あたりに進む距離を示します。
例:ドリルが1回転で0.1mm進む場合、送り量は0.1mm/revです。この単位は「ミリ パー レボリューション」と読みます。
また、「min-1」は回転速度を表すSI単位(国際単位)です。これは1分間に何回転するかを示し、例えば「1000min-1」は1分間に1000回転することを意味します。ただし、正確にはmin-1は「1分あたり」を意味するため、回転に限らず様々な速度の表現に使用されます。
ドリル歩行現象(ウォーキング現象)とは?
ドリル歩行現象とは、本来円形であるべき穴の断面が三角形や五角形などの奇数の多角形になってしまう現象です。ドリルの二枚の切れ刃にかかる切削抵抗のアンバランスによって発生し、穴の入り口付近に顕著に現れます。穴の形が「おむすび」に似ていることから「おむすび穴」とも呼ばれます。また、「みそすり現象」や「加工穴多角化現象」と表現されることもあります。
歩行現象の詳細なメカニズム
歩行現象は、ドリルの僅かな振れや被削材との接触状態の不安定さから始まります。 具体的には、以下の様なメカニズムで発生します。
- ドリル先端のチゼルエッジが被削材に接触すると、わずかな振れや切れ刃のアンバランスにより、左右の切れ刃にかかる切削抵抗に差が生じます。
- 切削抵抗の大きい側の切れ刃がより深く食い込み、ドリルは回転中心からずれた位置で回転を始めます。
- この状態から反対側の切れ刃が被削材に接触すると、今度はそちら側に回転中心が移動します。
- このサイクルが繰り返されることで、ドリルは楕円運動をしながら穴を切削していきます。
- 穴が深くなるにつれて、ドリルのマージンと穴壁との摩擦抵抗により振動はやや減衰します。
さらに、ドリル歩行現象に伴い、穴の内壁にらせん状の傷(ライフリングマーク)が発生することがあります。ドリルが1回転するごとに切削抵抗のアンバランスが振動の位相をずらし、それが螺旋状の模様として現れる現象です。
ドリル歩行現象が引き起こす問題点
ドリル歩行現象は、外観不良だけでなく、以下のような問題を引き起こす可能性があります。
- 穴径の拡大: 口元が広いロート状になり、設計値よりも大きな穴径になることがあります。
- 後工程への悪影響: ライフリングが残った状態でリーマ加工やタップ加工を行うと、精度不良が発生しやすくなります。
- ドリル寿命の低下: ステンレス鋼などの加工硬化しやすい材料では、工具の摩耗が激しくなります。
対策1:機械の状態を見直す
<ドリル剛性、ワークの固定、コレット取付精度の重要性>
機械側の対策としては、まず第一に、ドリルやワークの固定状態、そして機械自体の剛性を高めることが重要です。
- ドリル剛性の確保: 特に剛性の弱いハイスドリルやロングドリルは歩行現象が発生しやすいため、可能な限り剛性の高いドリルを選択しましょう。深穴加工でなければ、短いスタブドリルは有効な選択肢となります。ドリルをつかむ位置も留意。
- ワークの固定: ワーク(被削材)がしっかりと固定されていない場合、加工中に振動が発生しやすくなりますので、歩行現象を誘発する可能性があります。Tスロットナット、バイスやクランプを適切に使用し、ワークをしっかりと固定しましょう。
- コレット取付精度の確認: コレットチャックの摩耗や汚れは、ドリルの振れに繋がります。 定期的に清掃、メンテナンスを行い、精度を保ちましょう。 必要であれば新品への交換も検討してください。
<ガイドの使用>
既に開けた穴を利用したりガイドブッシュを利用することで、自己求心性が向上し、歩行現象を抑制することができます。
対策2:ドリルの状態を見直す
<正しい研磨を行う>
ドリルの研磨状態は、歩行現象に大きく影響します。
- ドリル研磨機の活用: チゼルポイントの偏心やリップハイト、ポイント形状の不揃いは、歩行現象を招きやすいため、可能な限りドリル研磨機を使用して正確な研磨を行いましょう。
- 切れ刃形状の見直し: 切れ刃の形状を適切に設計することで、歩行現象を抑制できる場合があります。例えば、チゼルエッジの中央部分をわずかに尖らせることで、歩行現象を軽減できることがあります。
<シンニング(スプリットポイント)>
ドリルのシンニングは、必ずしも歩行現象の抑制に効果的であるとは言えません。場合によっては、シンニングによって歩行現象が悪化する可能性もあるため、注意が必要です。
なお、短くなったドリルはチゼル幅が太くなっているため、先端部に刃を付けるシンニングは有効となります。
特殊なシンニング加工がされた月光ドリルはおすすめです。
ステンレス用月光ドリルストレートと六角軸月光ドリルであればビッグツールに依頼して再研磨してもらうことが可能です。ただし、長さが元々の3分の1以上でないといけないようです。
http://www.bictool.com/gekko/product.html#saikenma
ツイストドリルではなく、ミヤナガのコンクリート用のように、3枚刃ドリルを使用すると先端が安定します。ただし、再研磨が容易でなく経済的ではありません。
<チゼル角>
チゼル角(のみ刃角)は、歩行現象に大きく影響します。チゼル角が大きいと、三角形のふれまわりが持続します。チゼル角が小さければ歩行現象は発生しにくくなります。これはチゼル角が小さい方が、切削抵抗が内側に向かい、ドリルの動きが拘束されるためです。最適なチゼル角は、被削材や加工条件によって異なりますが、歩行現象に悩まされている場合は、チゼル角を小さくしてみるのも有効な手段です。ただし、90度以下に小さくしてしまうと切れにくいドリルになってしまいます。歩行現象を抑えたい場合は100°から115°がおすすめです。
<逃げ角>
逃げ角を小さくすることで、歩行現象を抑制できる場合があります。逃げ角が小さいと、切れ刃がワークに接触する面積が増加し、ドリルの安定性が増すためです。ただし、逃げ角を小さくしすぎると、切削抵抗が増加し、切り刃と逃げ面が摩耗して工具寿命が短くなる可能性があるため、注意が必要です。逃げ角が大きい場合はよく切れますがビビりが発生し、歩行現象になりやすいです。切り刃も欠けやすいです。歩行現象を抑えたい場合は7°から10°がおすすめです。当たり前ですが、逃げ角が負の角度になってしまうと全然切れなくなってしまいます。
<先端角>
ドリルの先端角は、検証のとおり歩行現象に対して大きな影響を与えません。被削材に合った角度を設定しましょう。
<下穴と皿穴、センターポンチ>
- 下穴:下穴は歩行現象自体を抑制する効果はあまりありません。場合によってはスラスト力が低下して歩行現象が発生しやすくなることがあります。ひずみ辺は5角形、7角形、9角形~になるでしょう。
- 皿穴:あらかじめ正確な皿穴加工を行うことで、ドリルの逃げ面が確保され歩行現象を抑制できる場合があります。
- センターポンチ:センターポンチを打つことで、ドリルの初期位置を安定させることができます。 ただし、センターポンチの痕がなくなると再び現象が発生しますので、他の対策と組み合わせて実施する必要があります。
対策3:切削条件を見直す
<回転数>
回転数の大小は、多少の変動はありますが歩行現象に対して大きな影響を与えません。
<送り量>
送り量を適切に設定することで、歩行現象を抑制できる場合があります。送り量が小さすぎる場合は、切れ刃のホーニング部で加工してしまうため、歩行現象が発生しやすくなりますので、送り量を大きくしてみましょう。
送り量の増加に伴い真円度が向上しますが、最適な送り量は、被削材やドリル径、加工条件によって異なるので、調整してください。
ドリル歩行現象は、様々な要因が複雑に絡み合って発生します。
上記を参考に、機械の状態、ドリルの状態、機械設定を適切に見直すことで、高精度な穴あけ加工を実現しましょう!